Table of Contents
3D printing, also known as additive manufacturing, has emerged as a transformative technology in the manufacturing sector, offering unprecedented capabilities for designing and producing complex parts and products. By building objects layer by layer from digital models, 3D printing is reshaping traditional manufacturing processes, driving innovation, and creating new opportunities across various industries. This article explores how 3D printing is revolutionizing manufacturing, highlighting its key advantages, applications, and the future potential of this technology.
1. Advantages of 3D Printing in Manufacturing
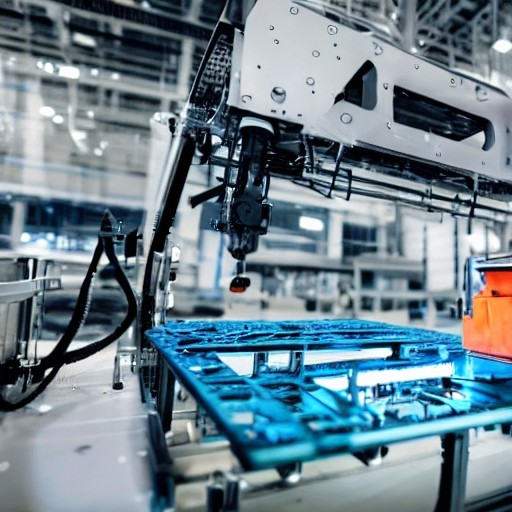
1.1. Rapid Prototyping and Development
One of the most significant advantages of 3D printing is its ability to accelerate the prototyping and development process. Traditional manufacturing methods often involve lengthy and costly prototyping cycles, requiring the creation of physical molds and tooling. In contrast, 3D printing enables rapid iteration by allowing designers to quickly produce and test prototypes without the need for expensive tooling.
This speed and flexibility in prototyping lead to faster design cycles, reduced development costs, and the ability to bring products to market more swiftly. For example, companies in the automotive and aerospace industries use 3D printing to develop and test new components, accelerating innovation and improving product performance.
1.2. Customization and Personalization
3D printing excels in producing customized and personalized products, catering to individual preferences and requirements. Unlike traditional manufacturing, which often involves mass production, 3D printing allows for the creation of bespoke items with minimal additional cost.
This capability is particularly valuable in industries such as healthcare, where customized medical devices, prosthetics, and implants can be tailored to individual patients. For instance, 3D-printed prosthetic limbs can be designed to fit precisely and comfortably, improving the quality of life for users.
1.3. Complex Geometries and Lightweight Structures
Traditional manufacturing methods often struggle with producing complex geometries and intricate designs due to limitations in tooling and machining. 3D printing, however, enables the creation of complex shapes and structures that would be challenging or impossible to achieve with conventional methods.
This capability is especially advantageous in industries such as aerospace and automotive, where lightweight and high-performance components are crucial. 3D printing allows for the production of lattice structures, internal cavities, and optimized geometries that reduce weight while maintaining strength and functionality.
1.4. Reduced Waste and Sustainability
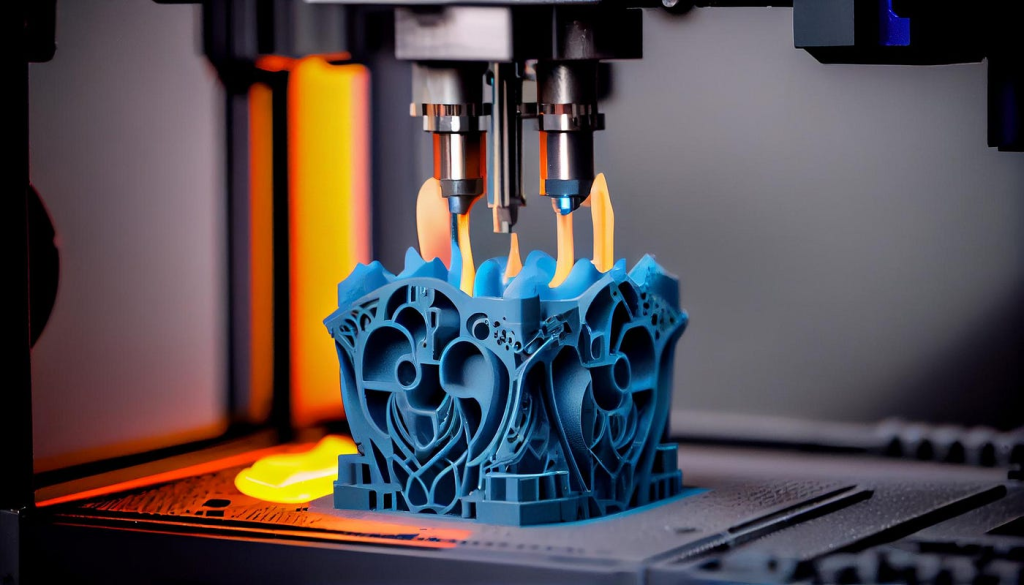
3D printing is inherently more sustainable than traditional subtractive manufacturing methods, which involve cutting away material from a larger block, often resulting in significant waste. In contrast, 3D printing adds material layer by layer, using only the amount necessary to create the final product.
This reduction in material waste contributes to more sustainable manufacturing practices and can lower costs. Additionally, 3D printing enables on-demand production, reducing the need for large inventories and minimizing overproduction, further supporting sustainability efforts.
2. Applications Across Industries
2.1. Aerospace and Defense
In the aerospace and defense industries, 3D printing is revolutionizing the production of high-performance components and parts. The ability to create lightweight and complex geometries is particularly valuable for aircraft and spacecraft, where weight reduction is critical for fuel efficiency and performance.
Companies like Boeing and Lockheed Martin use 3D printing to produce components such as turbine blades, fuel nozzles, and structural parts. This technology also enables rapid prototyping and testing of new designs, accelerating the development of advanced aerospace systems.
2.2. Automotive
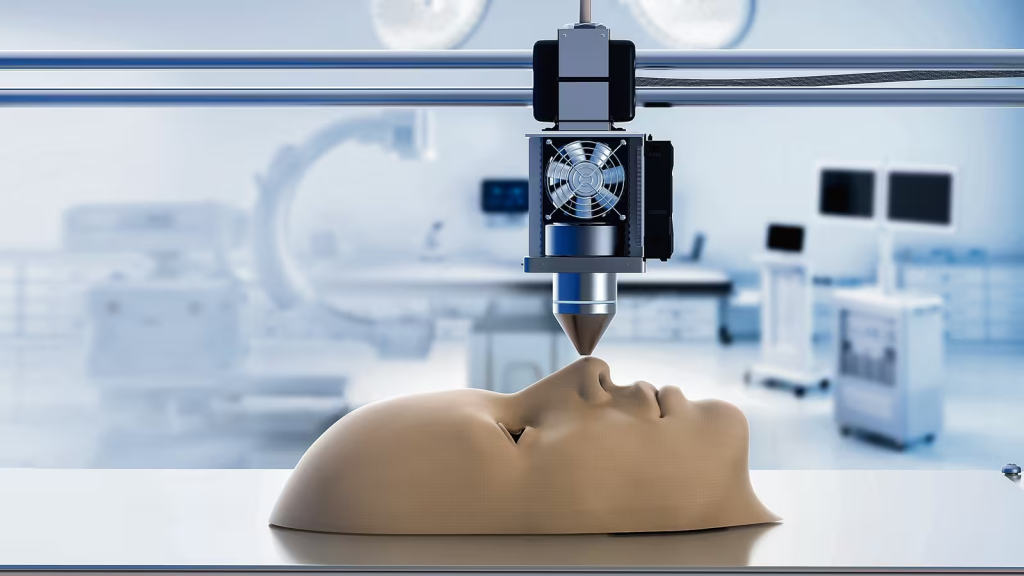
The automotive industry is leveraging 3D printing for both prototyping and production. Automakers use 3D printing to create prototype parts for testing and validation, allowing for faster design iterations and reduced development times.
3D printing is also being used for on-demand production of spare parts and customization of vehicle components. For example, BMW has implemented 3D printing to produce low-volume, customized parts for its vehicles, improving efficiency and reducing inventory costs.
2.3. Healthcare
In healthcare, 3D printing is transforming the production of medical devices, implants, and prosthetics. The ability to create patient-specific implants and prosthetics ensures a better fit and improved functionality.
3D printing is also used to produce anatomical models for surgical planning and training, allowing surgeons to practice complex procedures on accurate replicas of patients’ anatomy. This technology enhances precision and outcomes in medical treatments and procedures.
2.4. Consumer Goods
The consumer goods industry is exploring 3D printing for producing customized products and limited-edition items. Companies in fashion, jewelry, and home decor are using 3D printing to create unique designs and personalized items that cater to individual preferences.
For instance, 3D-printed footwear allows for customized designs and fittings, providing consumers with tailored products that enhance comfort and style. Similarly, 3D-printed home decor items offer a level of personalization and creativity that traditional manufacturing methods struggle to achieve.
3. Future Potential and Challenges
3.1. Future Potential
The future potential of 3D printing is vast, with ongoing advancements in materials, technologies, and applications. Emerging areas such as bio-printing, where living tissues and organs are printed for medical purposes, hold promise for groundbreaking developments in healthcare.
Additionally, the integration of 3D printing with other technologies, such as AI and robotics, could further enhance manufacturing capabilities and efficiency. As 3D printing continues to evolve, it has the potential to transform not only manufacturing processes but also supply chains, business models, and consumer experiences.
3.2. Challenges
Despite its advantages, 3D printing faces challenges that need to be addressed. These include limitations in material choices, build size constraints, and slower production speeds compared to traditional methods for high-volume manufacturing.
Moreover, intellectual property concerns and regulatory considerations must be navigated as 3D printing technology becomes more widespread. Ensuring the quality and consistency of 3D-printed products is also crucial for maintaining industry standards and consumer trust.
Conclusion
3D printing is revolutionizing the manufacturing industry by offering rapid prototyping, customization, complex geometries, and reduced waste. Its applications span diverse sectors, including aerospace, automotive, healthcare, and consumer goods, demonstrating its versatility and impact. While challenges remain, the ongoing advancements in 3D printing technology hold significant promise for transforming manufacturing processes, driving innovation, and shaping the future of production. As this technology continues to evolve, its role in revolutionizing manufacturing will undoubtedly expand, unlocking new possibilities and opportunities across industries.